Composites – design and production services for industry
SpaceForest offers cutting-edge solutions in fiber-reinforced composite materials, providing exceptional strength combined with minimal weight. Industries, including aerospace and defense, use our composites in their most demanding applications. By utilizing reinforcement materials such as carbon fiber, glass fiber, Kevlar®, and other fiber, our solutions meet stringent quality standards, ensuring reliability and durability in the most extreme conditions.
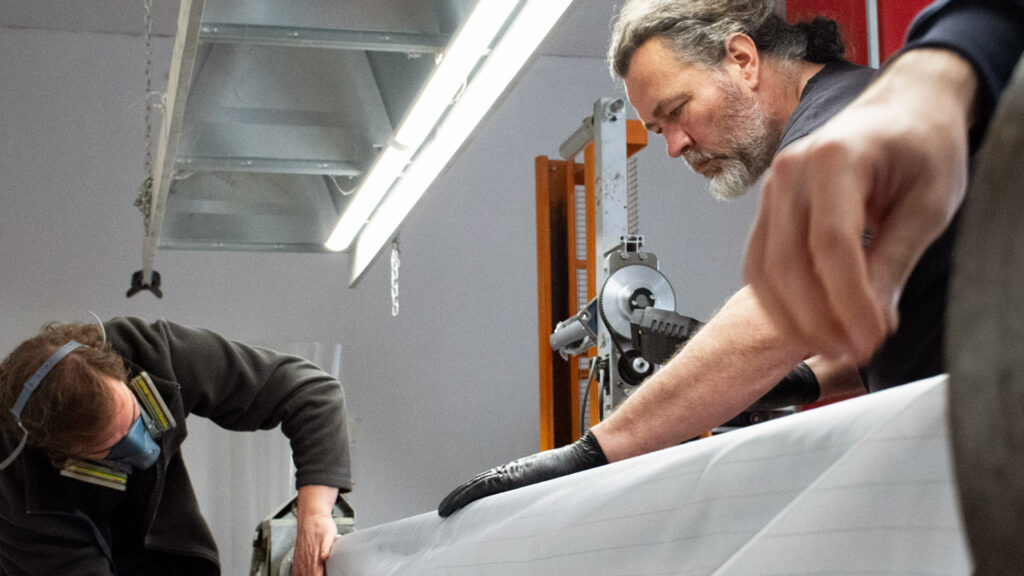
We design composite materials to meet our clients’ specific requirements. We adapt production technologies like filament winding, resin infusion, RTM (Resin Transfer Molding), and vacuum bagging. SpaceForest specializes in the production of lightweight and durable materials for industry.
Our competencies and potential applications of composites
At SpaceForest, we have extensive knowledge and experience in composites. This expertise enables us to provide innovative and durable solutions tailored to the needs of various industries. We create specialized composite components tailored to meet the specific technical and environmental requirements of our customers.
Composite tubes and nozzles
We offer custom-designed composite tubes and nozzles for rockets and spacecraft’s, providing high strength and resistance to extreme thermal conditions.
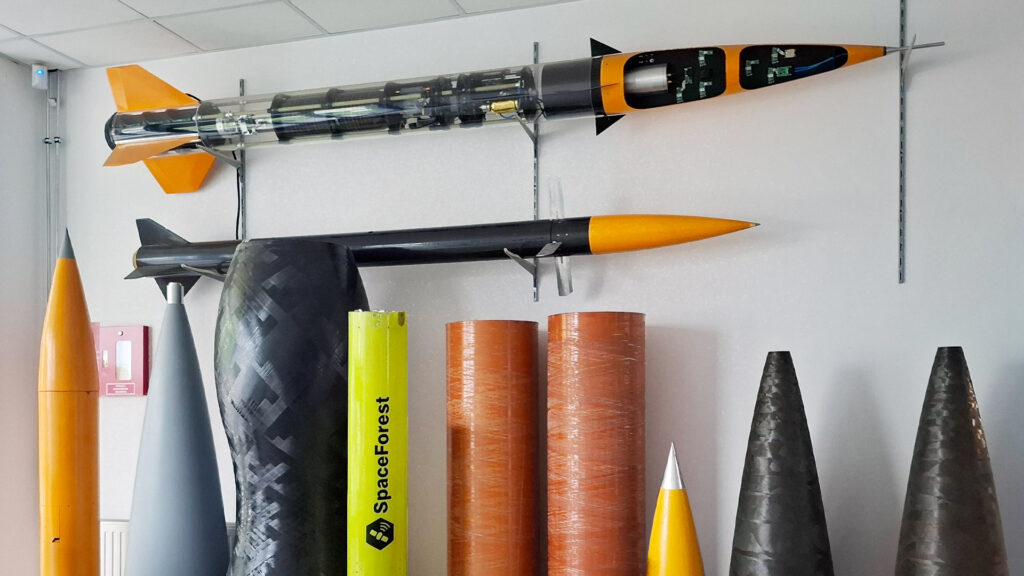
Electronic enclosures
We craft our precision-made electronic enclosures from composite materials, providing minimal weight without compromising protection. We tailor the designs to meet the specific needs of electronic components and environmental requirements. Depending on the material used, we can also adjust the enclosure’s radio transparency, ensuring optimal signal performance where needed.
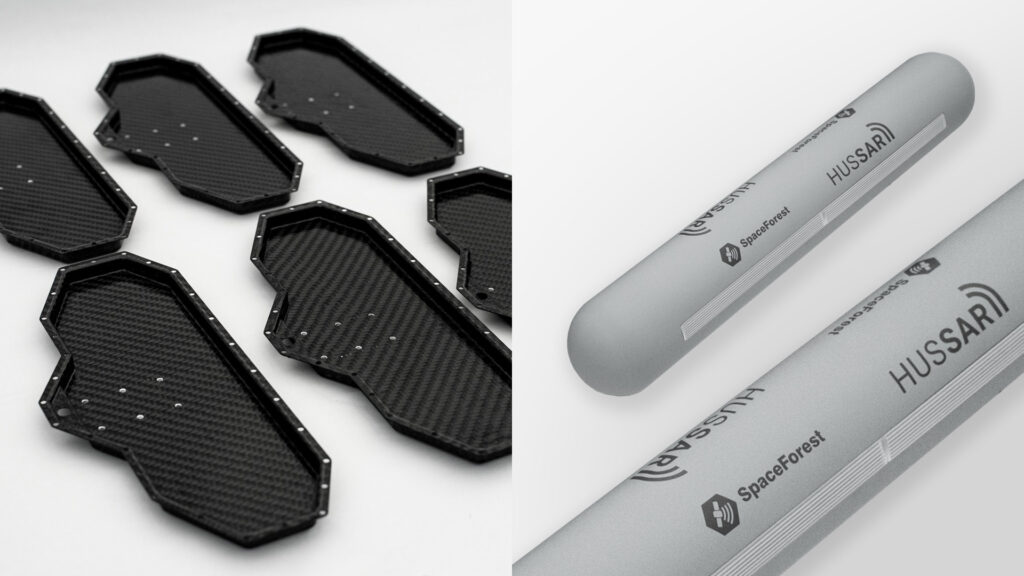
CNC machining services
Our high-precision CNC machining services create complex shapes and components. We work with carbon, glass, and aramid fiber-based composites (Kevlar).
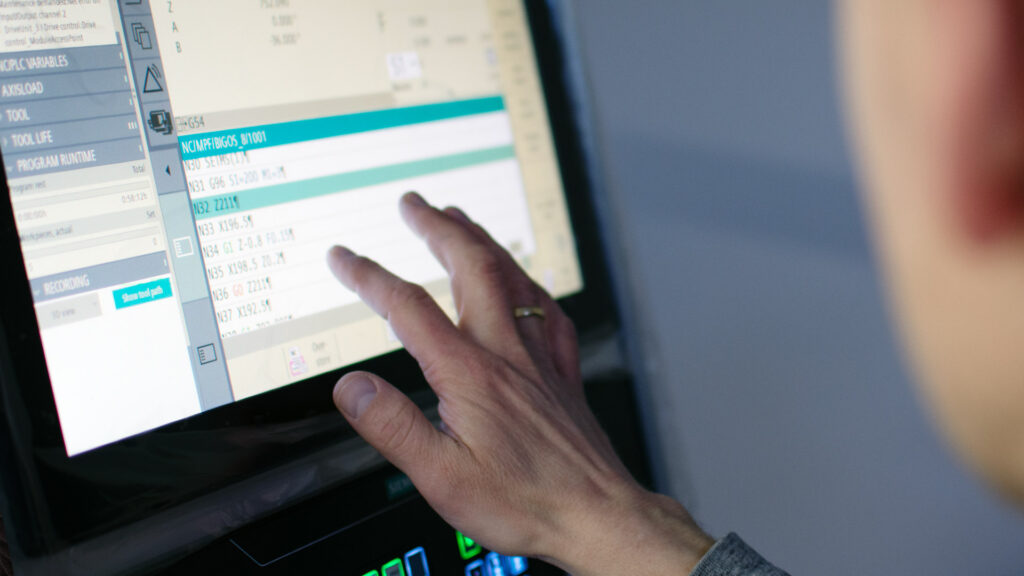
Materials we use in composite manufacturing – overview and applications
Materials used in composite manufacturing enable the creation of lightweight, durable, and corrosion-resistant products capable of withstanding extreme conditions. Industries widely apply them in aerospace, automotive, construction, sports equipment, and the defense and space sectors. Companies like SpaceForest, which develops advanced technologies for the space industry, benefit from composites’ efficiency, durability, and reliability. Composites are revolutionizing modern manufacturing, offering innovative solutions for advanced technological applications in demanding fields like space exploration and defense.
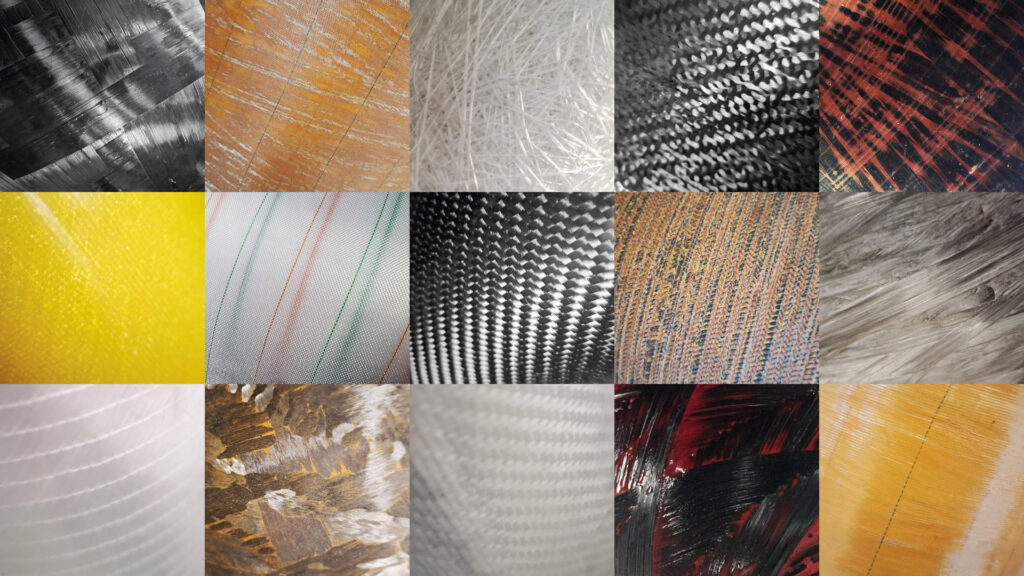
Carbon fiber
- Characteristics: Extremely high mechanical strength, stiffness, and resistance to high temperatures.
- Applications: Ideal for aerospace, space, and extreme condition applications such as rocket nozzles and aircraft structures.
Glass fiber
- Characteristics: Excellent corrosion resistance, high strength, and good electrical insulation at a relatively low cost.
- Applications: Widely used in construction, machine enclosures, wind turbines, and boats.
Aramid fiber (Kevlar®)
- Characteristics: Exceptional tensile strength, high impact resistance, and mechanical durability.
- Applications: Used in high-protection applications such as ballistic shields, military equipment, and impact-resistant components.
Basalt fiber
- Characteristics: Excellent resistance to oxidation, chemicals, and corrosive environments.
- Applications: Perfect for structures exposed to extreme environmental conditions, such as pipes, chemical tanks, and bridge structures.
Ablative composites
- Characteristics: Designed to withstand extreme thermal and mechanical loads, capable of absorbing and dissipating heat energy through ablation.
- Applications: Primarily used in rocket engine nozzles and thermal shields for spacecraft, especially in applications with extreme temperature requirements.
These advanced materials enable the creation of composites with unique properties. They are applicable across various industries that require exceptional strength, lightness, and resistance to different working conditions.
Our composite production methods
Resin Infusion
Resin infusion is a composite manufacturing process. It involves impregnating dry reinforcing materials, such as glass, carbon, or aramid fiber, with liquid resin. This is done under vacuum. This method ensures even saturation without air bubbles, delivering high-quality laminates. Manufacturers widely use resin infusion in the aerospace, automotive, and marine industries, where material lightness and strength are key.
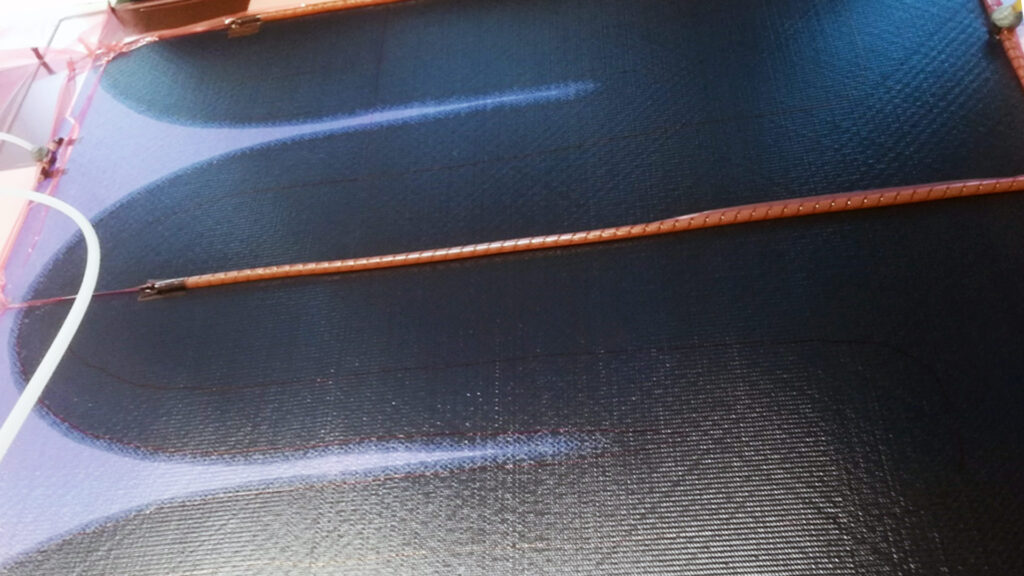
Vacuum bagging
In composite production, manufacturers use vacuum bagging. This technique involves applying resin to the reinforcing material. The assembly is then sealed in a vacuum bag, and the air is removed. This process improves resin penetration into the fibers and eliminates excess resin. As a result, it enhances strength and reduces the weight of the final product.
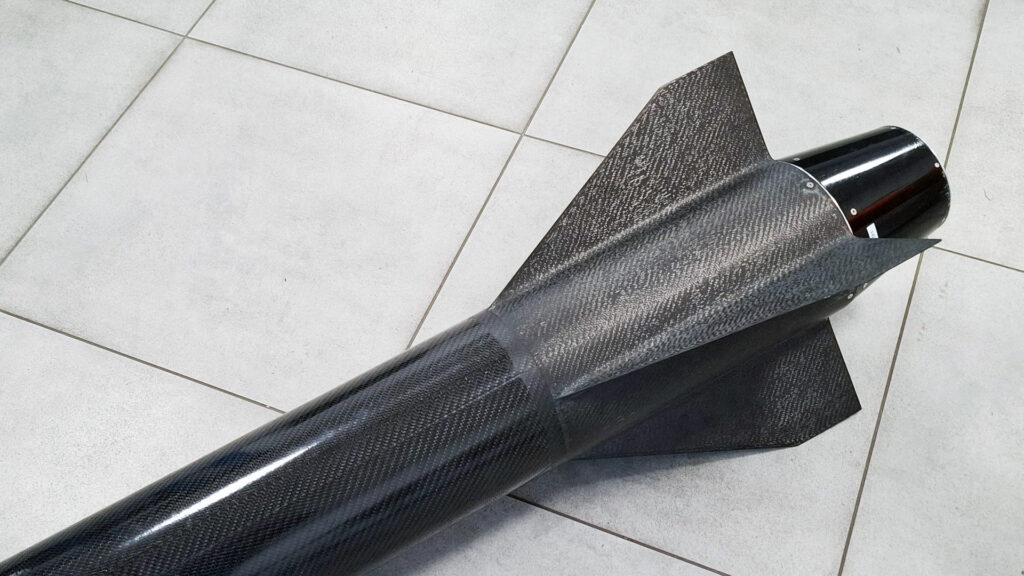
RTM (Resin Transfer Molding)
Manufacturers use Resin Transfer Molding (RTM) as an advanced composite manufacturing process in which they inject resin under pressure into a closed mold containing the reinforcing material. This method allows them to control the product’s thickness and shape precisely, making RTM ideal for producing high-quality, complex-shaped components. Industries commonly using this technique include automotive, aerospace, and sports equipment.
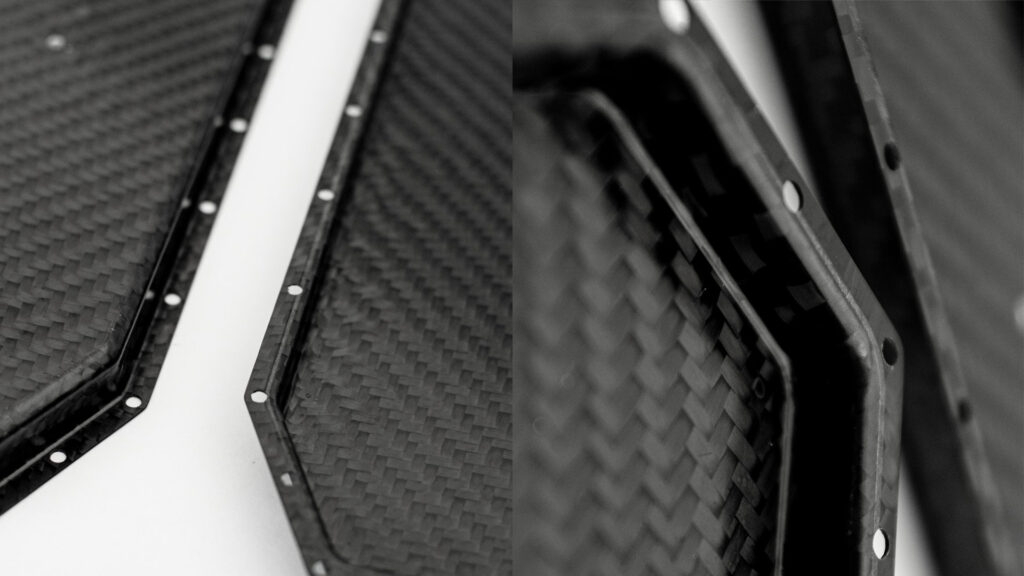
Filament Winding – Multifunctional Rotating Machine for Composite Winding and Processing
Our advanced filament winding technology enables the production of large composite structures with precisely arranged fibers for maximum mechanical properties. SpaceForest uses filament winding as a key technology to manufacture advanced composites that offer high mechanical strength and minimal weight. This process involves the precise placement of fibers in the form of rovings, creating a perfectly fitted structure with optimal mechanical properties.
State-of-the-Art winding machine
The service is provided on a state-of-the-art winding machine, a proprietary solution developed as part of a research and development project co-financed by the National Centre for Research and Development (NCBR). It is currently the largest and most advanced machine of this type in Poland. This innovative technology allows us to efficiently produce composite elements with rotational symmetry, including large pressure vessels, rocket bodies, ablative nozzles, combustion chambers, pipes, shafts, and axles. By changing the working tool, the machine can also function as a CNC lathe-milling machine, enhancing versatility and expanding its applications. This enables us to meet diverse production needs with greater precision and flexibility.
Exceptional design for precision
The engineers designed the entire machine to prevent even the smallest vibrations. They achieved this by constructing a robust steel structure weighing over 13000 kg, which they mounted on a 60000 kg concrete foundation. This guarantees exceptional stability of the production process, which translates into unparalleled precision and repeatability.
Meeting demanding client expectations
The winder ensures exceptional precision and durability, and with dedicated software, we meet the expectations of demanding clients. This investment not only meets our production needs but has also expanded our custom services. As a result, we now cater to a wider range of clients and meet their specific requirements more effectively.
Ideal for complex composite elements
The machine is ideal for producing composite elements with rotational symmetry, such as large pressure vessels, rocket bodies, ablative nozzles, and rocket engine combustion chambers. Thanks to the winding machine and dedicated software, we are capable of handling even the most demanding projects, where quality and durability are critical, which we tested on the bodies of the suborbital PERUN rocket and the supersonic VIRA.
Technical specifications of the multifunctional rotating machine | |
Working area | ø=1400 mm x l=8000 mm |
Number of rovings | Up to 10 simultaneously |
Maximum tension | 200 N per roving |
Maximum support speed | 1.6 m/s |
Maximum roving feed rate | 2.5 m/s |
Maximum weight of the part | 2000 kg |
Heating capacity in the chamber | up to 200°C |
Operating modes | Filament winding, Lathe, 5-axis milling machine |
Watch our filament winding machine in action: composite tube manufacturing
Below is a video showcasing our filament winding machine in action during the production of a composite. Watch as precision fiber winding creates a lightweight and durable structure, demonstrating advanced composite manufacturing technology.
Do you have questions or are you interested in our composite offer?
Contact us to discuss our advanced composite solutions. They combine exceptional strength with minimal weight for demanding industries like aerospace and defense. Our tailored production processes ensure reliability in extreme conditions. We look forward to collaborating with you to enhance your projects!